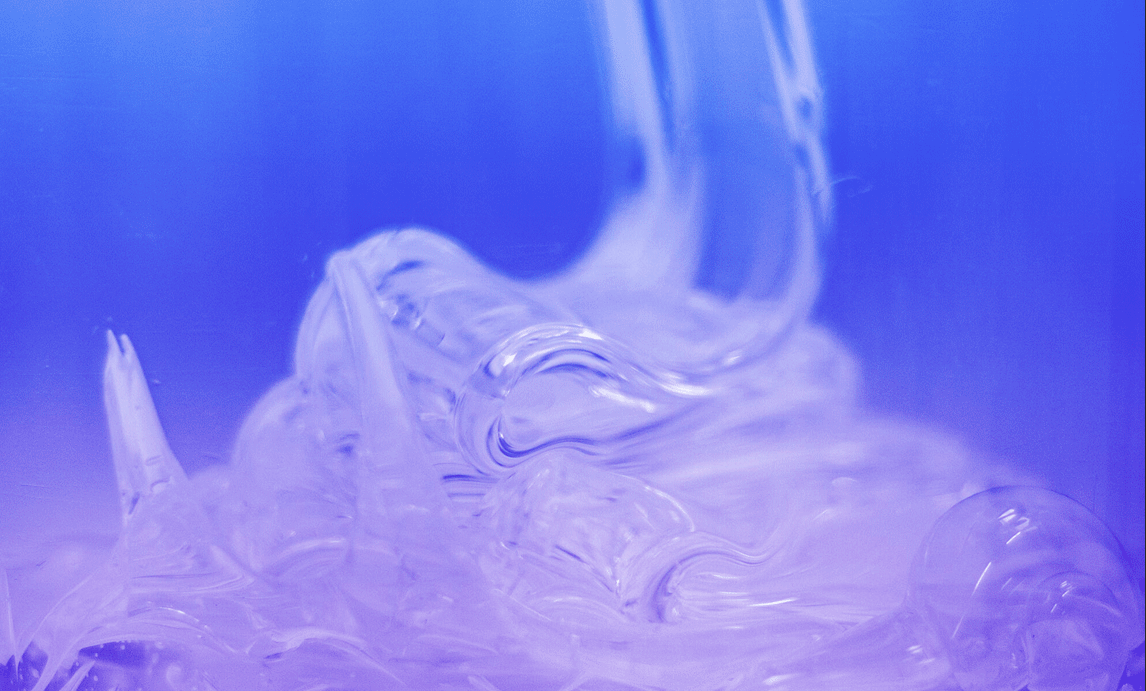
Medical technology is a broad field, encompassing instruments, apparatus, appliances, software, implants, reagents, materials, and other articles. Medical technology could refer to a small yet lifesaving implant or a much larger instrument used within hospital procedures like fluid management and respiratory support.
In addition to sustaining and saving lives, there are many medical devices designed specifically to enhance a patient’s quality of life. Prosthetic limbs can assist amputees to live unhindered by their so-called disabilities, while surgical implants help many breast cancer survivors regain confidence post-mastectomy. In the field of diagnostics, a range of medical devices help doctors and patients screen for disease and infection. Even a wound care product, simple at first glance, lies within the complex field of medical technology.
The list goes go on, expanding every year as innovative medical device OEMs develop new technologies to improve patient care. For context, the World Health Organisation estimates that there are 2 million different kinds of medical devices on the world market, categorised into more than 7,000 generic groups.
Many different materials are used to achieve the various components needed within this array of devices – from metals like titanium to thermoplastics, ceramics, tissue-engineered medical products, and biologic materials. While each material has its individual advantages for specific end-uses, one material stands out for a different reason: its versatility.
The silicone advantage
Silicone finds applications across most fields of medical technology, including all the aforementioned areas and many more besides. The medical sector’s earliest use of the synthetic polymer was to coat glassware and needles. Over the past 60 years, OEMs have used silicone in the manufacture of many implanted medical devices, as well as orthotics, prosthetics, dental, wound care, diagnostics, and drug-eluting devices.
Medical-grade silicone is stable in extreme temperatures and resistant to chemical and thermal degradation. Being soft to the touch and conformable, silicone offers comfort to patients whether applied on or under the skin. The material’s hydrophobicity makes it an effective lubricious coating for surgical tools and syringes, meanwhile this water repellence helps ensure bacteria resistance too – a huge benefit for the medical industry. Most importantly, silicone is a proven, biocompatible material, and it’s this chemical inertness that makes silicone safe to use in long-term implants.
It’s easy to see why silicone has become a go-to for the medical industry. And its versatility takes the material’s potential to a whole other level. To explore this, let’s take a look at the different types of silicone technologies used by the med tech industry.
Types of medical-grade silicone
Liquid silicone rubber (LSR) is a popular choice. It is typically used within injection moulding machines, where it cures completely and quickly to create complex parts with fine detail, tight tolerances and low shrink rates.
High consistency rubber (HCR) has a higher viscosity and is better suited to high-strength moulding and extrusion processes. Overall, the performance characteristics of LSR and HCR can be similar and each material boasts a huge variety of medical applications. The choice between them usually comes down to required physical characteristics and manufacturing method.
Other forms of silicone have adhesive properties, making them a great sealing solution for applications where high-strength elastic bonds between substrates are needed. These same properties add another medical application to silicone’s long list: skin adhesion. Used across wound care, medical tape, and transdermal drug delivery patch products, silicone adhesives provide reliable yet non-traumatic and hypoallergenic adhesion to skin.
Medical-grade room temperature vulcanising (RTV) silicone comprises a two-part system that can be easily mixed and cured into soft yet durable elastomers. Ideal for prosthetic liners, orthotic inserts, bandages, and shoe insoles, RTVs provide comfort and biocompatibility in the manufacturing of soft parts in contact with a patient’s skin.
Silicones are also available in gels and fluids. Gels are very soft elastomers for the manufacturing of cushions and breast forms, meanwhile silicone fluids are made from polydimethylsiloxanes fluids, emulsions and RTV lubricants, and are used to coat and lubricate drug delivery devices and surgical tools.
Exploring silicone’s potential
For a full selection of medical-grade silicone technologies, medical device OEMs can explore Elkem Silicones’ Silbione™ range of LSR, HCR, silicone adhesive, silicone skin adhesive, RTV, silicone gel, and silicone fluid products.
So versatile is silicone that individual devices can use these materials in more ways than one. Taking a wearable device as an example, Philipp Schattling, Elkem’s project leader for diagnostics and long-term medical implants, explains: “Wearable devices consist of many different components and many different building blocks, and every building block may require different properties and performance characteristics.
“This can be a challenge because usually with just one technology you cannot address each and every requirement. The benefit of silicones is that they cover a broad range of different technologies. We have the glue, the sealant, the adhesive, the LSR for the housing, and the HCR for the tubing.”
Wearables are a key trend in the medical industry, and silicone will play an important role in their continued research and development. Meanwhile, the material is enabling many other important healthcare trends such as point-of-care diagnostics, minimally invasive surgery, and patient-customised medical devices enabled by advancements in 3D printing technology.
To find out more about silicone’s role in these exciting trends, download the whitepaper below.