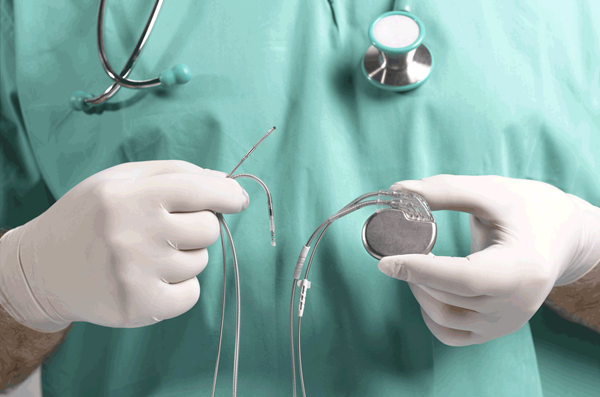
Medical-grade silicone’s greatest advantage is its versatility. Used in implanted medical devices, orthotics, prosthetics, diagnostics, and dental and wound care to name but a few, the applications are endless. In some of the very latest innovations, silicone is even being used for 3D printing of patient-customised medical devices.
Reasons for this popularity are clear. Medical-grade silicone is durable, stable in extreme temperatures, and resistant to chemical and thermal degradation. It is also hydrophobic, which makes it an effective lubricious coating and helps with bacterial resistance.
Most importantly, silicone has been proven to be a biocompatible material and chemically inert, making it safe to use in long-term implants. Silicone is also comfortable for patients, being soft to the touch, whether applied on or under the skin.
Drug-eluting devices
Drug-eluting devices are another key application that benefit from silicone’s properties. Implantable drug delivery devices deliver an active pharmaceutical ingredient (API) to a treatment area with sustained release over time, with advantages including targeted drug delivery, lowered systemic toxicity, minimised drug dosage, and eliminated reliance on patient compliance.
Silicone forms a permeable matrix structure when cured, thus creating space for APIs to reside and pass-through over time. There are three basic methods for silicone to interact with an API in an implantable device: blending of the API into the raw silicone prior to cure (forming a matrix), curing of the silicone into a form to act as a reservoir for an API, and impregnation of an API into a cured silicone component with the assistance of a solvent (a second way to achieve a matrix).
Blending an API into a raw silicone has the advantage of being able to prepare a large, homogenous batch of raw material at one time, enabling the consistent production of components. The application of heat to cure silicone can limit the API that can be used. A reservoir system can avoid the heat issue, but only if the targeted API is soluble.
Impregnation also sidesteps issues with heat, but again relies on an API being soluble in an organic solvent (such as toluene or chloroform). This process takes advantage of the swelling undergone by silicone in the presence of the solvents to allow the API to enter the silicone matrix. Controlling exact amounts of API loading via impregnation is not as precise as full blending into a raw material, and this approach is best suited for applications where exact release rates are non-critical.
Types of silicone
Sean McPherson, senior business development manager for Elkem Silicones, one of the world’s leading, fully integrated silicone manufacturers, points out that there are several different silicone types for drug-eluting devices, each with their own advantages and challenges.
McPherson explains: “You have Higher Consistency Rubbers, you have Liquid Silicone Rubbers, and then Adhesive materials – and there’s an array of different cure systems. If you need a lower temperature cure because the API is very sensitive to temperature, that can be done.”
HCRs (High Consistency Rubber)
HCRs in implantable drug devices have some advantageous physical properties compared to other silicone types, including tensile strength, elongation, and tear strength.
HCRs are most suitable for extrusion due to their “green strength”, which enables the holding of inner lumens within the tube while heat is being applied to cure the material. Its continuous process lends itself to automated cutting and fast production. Co-extrusion of drug loaded silicones over various substrates, such as other cores or wires, is also possible.
Typically, extruded drug loaded silicone rods or profiles are created as part of an implantable drug delivery device. Silicone sleeves are commonly used to cover high-load-level drug cores to create reservoir systems, and HCRs in implants can also be calendared (to make sheeting) and moulded via compression or transfer processes.
However, with less ability to flow, geometries for moulded HCR parts need to be simple and this can lead to costly secondary operations. Achieving homogeneity of mix with a powder or liquid API will likely require a masterbatch (made with a small amount of the HCR and a high level of drug) which is then slowly blended in the main HCR batch. The process can be lengthy and requires thorough cleaning, increasing costs.
LSRs (Liquid Silicone Rubbers)
LSRs are mostly used in injection moulding, but some applications include compression and transfer moulding. LSRs are often fully blended with API and can be moulded into reservoirs of varying shapes or cured and impregnated with API.
LSRs possess the widest design potential, with the ability to flow into much smaller geometries than HCRs. Mixing APIs into LSRs is also simpler and achieving fully homogenous blends is more likely. API format (liquid, powder) is also potentially easier to mix directly into an LSR without the necessity for creating a masterbatch.
There are, however, challenges with LSRs. The stress of the injection moulding process can create heat, which is detrimental to API potency. Also, frictional heat can affect an API, as can curing the silicone in the mould. This challenge can be mitigated through an optimised silicone cure system, but this is generally a more extensive process and thus is best identified early in the design.
Adhesives
Adhesives are a complementary addition to an implantable drug device, added to a substrate such as thermoplastic, metal, or even another silicone. Adhesives can be deposited very accurately and the precise control in location and amount ensures that the correct amount of silicone-eluting API is placed exactly where it is needed. However, they are unsuitable as standalone drug eluting components.
Additionally, adhesives have a variety of cure mechanisms (condensation and addition cure, for example), providing options outside of heat curing – an advantage when working with APIs. However, these cure mechanisms take longer to cure than heat-based alternates, raising production times and cost.
Which silicone is right for your device?
Choosing between HCR, LSR, an Adhesive, or some modified version of the three, must balance factors such as physical performance, manufacturability, and API compatibility.
As McPherson notes: “If you have a complex structure that you need to form, something like a LSR can really do all kinds of things with the way it flows within a mould. You can do some very complex or over-mould applications. You can use an adhesive that would cure almost at room temperature, for instance, and you could just use that to add support structure when you’re putting your device together. That also does double duty and can elute the drug over time.
“There’s a lot of flexibility in there just depending on what the device or therapy needs to achieve.”
To discover more, please download below.