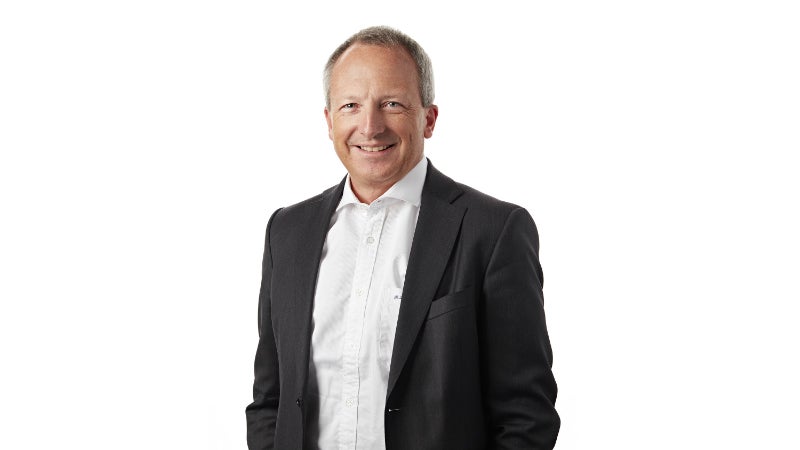
Rolf Rihs has been working at assembly system manufacturer Mikron Automation for nearly 17 years. Over that time, he has seen the changing needs of automation solutions and mass production, including regulatory requirements, the prevalence of generic drugs and the pressure of health costs. Medical devices are also becoming smaller, smarter and more complex, bringing further challenges to the industry.
He speaks to Medical Device Network about the key requirements of the disposable devices industry and how Mikron Automation meets these demands.
Rebecca Panks: What are the key requirements of the disposable devices industry and how do your solutions meet those needs?
Rolf Rihs: “I believe there are three key points to take into consideration. One is the regulatory side, especially the US Food and Drug Administration (FDA). The FDA is governing this market where there are clear guidelines, and these guidelines also have an impact on the automation side through the good automated manufacturing practice (GAMP5). If it is not the FDA, other regions apply.
“With the regulatory requirements, Mikron has been building automation equipment for devices since the early 90s, so we have had long experience. In the meantime, we have also built the respective know-how to deal with all those regulatory rules. Our documentation is adapted to that and this is something not all automation suppliers can deliver.
“The other thing that we have seen in recent years is generic drugs coming more and more into the market. That also has quite a strong impact on the industry of our customers and indirectly also on to us.
“The impact is simple, it is just mathematics: You usually have one pharma company who owns the patent and dominates the market, but now there are suddenly more players. More players mean that the volume for each player is somehow diluted and it is unknown who will win which market share.
“What Mikron offers in line with this; we have scalable solutions and we can support such new players from prototype stage to mass production. We offer solutions for all. That’s something which was not the case twenty years ago, because at that time the number of players and the number of different devices in the market was less.
“The last important point is, at the end of the day, health costs. Health costs are under pressure everywhere, and more and more health medications will come. This is very positive for the medical device manufacturers and also for us as automation suppliers.
“It’s not only the sales of medication, it’s also in the area of diagnostics. A few years ago, you went to the doctor, he took some blood, then you waited a week until he comes back with the results. Today, more and more, they try to close this loop.
“He needs quick diagnostic tools and they have devices in there; disposable devices, which are somehow similar to medical devices and where Mikron is also successfully active.
“With cost pressure, the reaction of the system involves self-medication, it involves quick diagnostics. There, once again, we have a lot of experience and we built automation systems for a lot of such devices before.
“Last but not least, we put a strong emphasis on innovation and trying to use the most modern technologies, which are adapted for those uses.”
RP: There is a trend in the medical device industry at the moment of personalised healthcare. Is this something that will affect your company?
RR: “Sure, it will affect us but when we look at those requirements of customers coming to us, as we are an automation system supplier. So far, we have not seen that personalisation on the level of medical devices. The personalisation is more on the level of what the drug is in the device, or if it is a smart device how this device is linked to software and to personalisation on this level.
“In other industries, there is this trend of personalisation also of physical products. But due to the regulatory restrictions of the medical industry, I don’t believe that in the near future personalised variants of the core functionalities of medical devices can be brought to the market.
“Personalisation can be expected on the outside look and certainly on the software parameters of electronic medical devices, for example, pen injectors for diabetes patients.”
RP: Throughout your time in the industry, how have you seen assembly manufacturing change in that time?
RR: “When I look at what has changed, one thing is very clear. Today’s medical devices are more complex. They are going in different directions. One direction is that they tend to become smaller because who wants to have an ugly big injector pen? They tend to be smaller and that makes the assembly more challenging. The more important axis that has changed is that some of the devices are becoming smart. ‘Smart’ meaning to have electronics inside and they are linked to some controlling devices. That was completely not the case 17 years ago.
“The consumer goods and electronics industries are used to quick changes but the medical industry was not used to this change. Again, the regulatory environment is also making such changes a lot more complex. What we see when we talk of smart devices is the link, the electronics, but also new sensors in those products and some of those sensors they are a completely new territory that the medical device companies never went into before.
“Luckily for Mikron, as we are at the top end of technology, we could grab a nice number of such new modern devices and could finally deliver to customers solutions in which these new technologies could work.
“So, more complex, smaller and smart is one axis I have seen. And the other axis I have seen in these 17 years is the number of rendered products, ultra high-volume devices, I believe is reducing. This is again linked to things I said before: the more players and also the wide range of drugs applied with medical devices. It is also maybe a little bit linked to what you said before of this personalisation. If one pen fits all, we have to maybe find different versions of pens that we use to set a volume per each device.”
RP: Do you find that it is linked to the changes in medicine; that things are getting more specific?
RR: “It is true, it is linked together. We are evolving, more and more are available. For example, if you compare today with when you were a child. This certainly applies for medical devices because when I was a kid, I cannot remember somebody using an inhaler or injector pen.”
RP: Are there any further industry changes you have noticed?
RR: “There is one change: the war for talent. It is today not easier, or to put it another way, it is more complex to find really good people who can deal with all those challenges. But that is not just applied to us as automation system suppliers, you can call and ask anybody, you will have the same issues.
“One effect we all have is there is a wider range of devices that means that the certainty that a device will become successful in the market becomes less today than it was maybe ten or 15 years ago. In the industry, they need to play on so many fields they never know exactly which of the horses will win. That means the amount of money they can invest on each horse is a little bit smaller.
“That means that instead of immediately going for a high-volume production line, they have to go with smaller volumes first, then ramp it up. That has two effects: they need scalable solutions and it does add the effect they need to cut the time-to-market.
“In the past, especially, we have seen in the medical industries that sometimes it takes forever until your product comes to the market and it puts huge pressure on this time-to-market. That’s a challenge for everybody.
“Another thing I guess we already touched a little bit, it is clear if you have variable devices or if you have quick diagnostic devices with new technology we have not seen before, adapting and really mastering those technologies is certainly a big challenge.”
RP: We spoke a little about the past and the present, so how do you see mass production changing in the future?
RR: “As I have already mentioned with this personalised devices, I do not believe that each and every injector pen or inhaler will be different. Mass production will survive, but the question is what volumes will there be? Things like, for example, the diabetes pens companies like Sanofi could launch in their groups and produce billions of devices. I guess that will become very difficult in the future.
“There will also in the future be devices that will be produced as annually in the millions of parts.
“And then on volumes, there is one other aspect. If you look in the whole world there are more than seven billion people. Out of those, there are more than 400 million which are diagnosed with diabetes, for example. How many of them have the privilege today to have an injector pen? Many of them are not treated at all. How many of them are still treated with reusable pens, which are less comfortable, or even with the old-style method where you take a syringe and you make your injection? So, in this aspect, there will also be changes.
“What I believe will not happen is that old equipment which is not used anymore in the US or in Europe in the medical device industry will move to some other countries to be reutilised. At least, when we look at the type of equipment we built. When I joined Mikron in 2002, we had a chance to develop our first high-volume diabetes pen assembly line.
“This line has now been working for 17 years, three shifts, five to six days a week. What happens now with this equipment? Did they scrap it in the meantime? No, it is still alive. And it has now moved from the company who purchased it at that time to another production plant and it will undergo a substantial upgrade programme.
“This is different to consumer goods, where the taste changes and then their equipment becomes obsolete because they need new ones, in the medical industries, those automation equipment normally have extremely long lifetimes. It is updated and upgraded again and again.”
RP: Another key trend is the use of artificial intelligence (AI) such as voice recognition to shared machine learning. How does that apply to Mikron and how do you anticipate that that might change?
RR: “The medical device industry is not a front-runner in this aspect because it is a very conservative industry and the regulatory hurdles make it move not too fast.
“You will not find artificial intelligence in medical devices in the very near future, I personally believe. In the health industry yes, to support doctors in their judgements, artificial intelligence will become very important. And also in the research of new drugs, artificial intelligence will become very important. In the down-to-earth production of medical devices, artificial intelligence will not bring many changes soon.
“But, it is always a question when you are talking about digitalisation what we are dreaming about. You take one of our machines. When it is running, it is generating a lot of data. The assembly equipment has actuators and a lot of sensors inside and this data in the past was always analysed and used to run the machine. And now it is clear that we can look at that data and say: ‘What are we doing with this data?’, ‘Can we apply some intelligence algorithms, as artificial intelligence is doing, and make a conclusion out of this data, which we were not able to do in the past?’. Yes, this is possible. Will it be used fast and in large-scale? No, I don’t believe so. Why? We are in a conservative industry, so getting access to data is challenging.
“The other thing is all of our equipment is customer-specific, so you have one type of this equipment only. The number of programmers of artificial intelligence you can afford to put behind those lines is limited.
“I mentioned this access to data, that is an area where we are struggling. Very often, when we deliver our production lines, we have no more access to the data because data security is in most companies’ minds. When we look then at pharma companies, they are sometimes like maniacs.
“Imagine, you are a pharma company and a hacker accessed your network and changed the recipe of a drug. You didn’t realise. Your drug, instead of being positive for the consumers, suddenly becomes negative for the consumers and that would be really the worst, worst-case scenario for a pharma company that could happen. So, what they are doing is they are cutting off their IT networks.
“In a medical device, if the setting of a medical device is done wrong, this device could deliver the wrong result to the patient. So, they are really determined to ensure that nobody can access and the easiest way to secure that is to cut off all access.
“I have been working in this industry after 17 years. Working here is fun and there are always new challenges coming. It is not boring work. It is really a very interesting job to build customer’s automation systems, which will fulfil the requirements of medical devices. For future talent, this is a good place to be.”