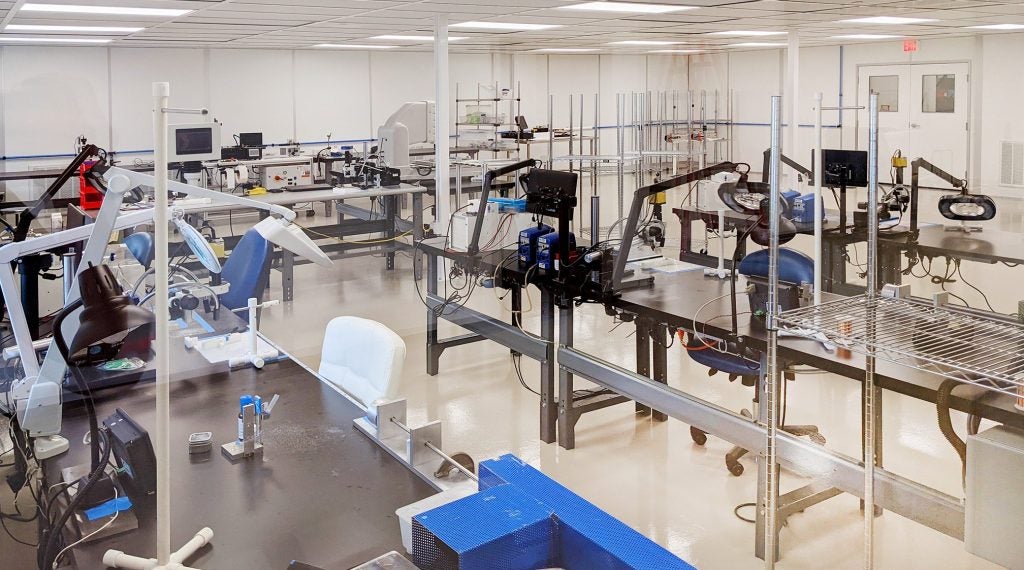
With the number of minimally invasive surgeries increasing every year[i], driven by lower costs and reduced impact on the patient, the medical device industry is driving the trend for ever smaller components suitable for such procedures. Meeting this need requires a CMO that can not only manufacture with precision and accuracy but also answer the need of designers that require expertise and agility in equal measure.
“Companies are constantly on a quest to come up with the next generation device,” says John Corsten, technical sales manager at Custom Wire Technologies (CWT), a contract manufacturer serving OEMs and researchers in the medical device industry, with over 20 years of experience specialising in custom designs.
This ability for customisation is vital for CWT’s customers, who can specify exactly what they need for their project, notes Corsten: “CWT works closely with the R&D engineers whose goal is to do a proof of concept, with hopes of getting validation and eventually going into full production.
“Everything we manufacture is custom to whatever the customers’ needs are. An off-the-shelf component isn’t going to yield the results they desire. Most of the time a custom component is required for the device to work as intended.”
How to make a custom component
Once a design has been finalised by the customer, CWT works with the OEM to get the design ready for manufacturing. “Our global sales team has a unique expertise with raw materials and that can lead us to making suggestions when warranted,” explains Corsten, “However, as a rule, CWT doesn’t interfere with the actual design of medical devices – we leave that up to the customer.”
Customers appreciate CWT’s advice on materials and manufacturing methods, Corsten points out: “Once prints/specs are presented to us, we will have an open conversation on whether what they are asking for is manufacturable. At that time, we are more apt to make suggestions on what we can manufacture on a repeatable basis.”
Super-elastic nitinol is trending
While custom wire coiling, grinding, forming and assembly are at the centre of CWT’s business, the company also sees trends in the materials and alloys being requested by customers.
“There is a continual upward trend in utilising the unique properties of nitinol,” says Corsten. “Nitinol coils and core wires continue to be a high growth area.”
The use of nitinol in the medical device industry has soared over the last decade. An alloy consisting of nickel and titanium, nitinol exhibits super-elasticity with ‘shape memory’ and is also corrosion resistant with excellent biocompatibility. It can take much more strain than stainless steel but can be challenging to work with. However, CWT has built up a wealth of experience working with the alloy.
Next generation medical devices
Corsten notes that CWT receives incredibly positive feedback from customers regarding their technical knowledge and customer service. “We take full advantage of being a small company (under 100 employees) in that we can pivot quickly,” he says. “There has been a trend in the device industry with contract manufacturers getting acquired. Once they become part of a much larger organisation, you can lose the agility that our customers want and need for quick turnarounds and excellent customer service.
“CWT is committed to sticking to our roots and never losing sight of what got us to where we are today, the customer. We are privileged to work with companies around the world on cutting edge technology that will eventually become the next generation medical device, saving countless lives. It is easy to take pride in your work when you know you are making a difference and it’s a constant motivation to get better and more efficient at what we do.”
Find out more about CWT’s custom wire services by downloading the whitepaper below.
[i] https://www.ncbi.nlm.nih.gov/pmc/articles/PMC9691544/#:~:text=In%202017%2C%2011.1%25%20of%20these,%25%E2%88%923.0%25)%2C%20respectively.